Question 1: Analyze the types of manufacturing processes and describe the importance of process selection in facility layout. Discuss the different types of facility layouts and their advantages and disadvantages. Describe assembly line balancing and closeness rating.
Answer: Manufacturing processes and facility layouts play a crucial role in the production of goods. The selection of the appropriate manufacturing process and facility layout can significantly impact the efficiency, productivity, and cost-effectiveness of production. Understanding the different types of manufacturing processes and facility layouts, as well as assembly line balancing and closeness rating, can help organizations make informed decisions when designing and optimizing their production systems
Manufacturing Processes:
There are several types of manufacturing processes, including:
- Continuous Processing: This involves the production of goods in a continuous flow, without interruption, and with a high degree of automation. Examples of continuous processing include oil refining, chemical production, and electricity generation.
- Batch Processing: This involves the production of goods in batches, where each batch is a specific quantity of the product. Batch processing is common in the production of pharmaceuticals, food and beverage products, and electronics.
- Job Shop Processing: This involves the production of goods in small batches or one-off items that require unique processes. Job shop processing is common in custom manufacturing, such as machine shops or metal fabrication.
- Cellular Manufacturing: This involves the organization of workers and machines into cells that produce a specific family of products. Cellular manufacturing is common in industries that produce a variety of similar products, such as automobile manufacturing.
Process Selection in Facility Layout:
Process selection is crucial in facility layout as it determines the flow of goods, the efficiency of production, and the cost of production. The selection of the manufacturing process must take into account the product design, demand for the product, available resources, and the skills of the workforce.
Facility Layout:
There are several types of facility layouts, including:
- Process Layout: This layout groups similar machines and activities together in departments, and products are moved from one department to another. The advantage of this layout is that it allows for flexibility in production and can accommodate a variety of products. However, it can lead to high material handling costs and long lead times.
- Product Layout: This layout arranges machines and activities in a linear sequence, and products move along a conveyor belt or assembly line. The advantage of this layout is that it results in high productivity and low material handling costs. However, it may not be suitable for a variety of products or product changes.
- Fixed-Position Layout: This layout is used in the construction of large products, such as ships, buildings, or aircraft, where the product remains in one location, and workers and equipment are brought to the product. The advantage of this layout is that it allows for the production of large, complex products. However, it requires a large amount of space and can result in high material handling costs.
Assembly Line Balancing:
Assembly line balancing is the process of assigning tasks to workstations along an assembly line in a way that minimizes idle time and maximizes productivity. The goal is to ensure that each workstation is utilized efficiently and that the assembly line operates at an optimal speed.
Closeness Rating:
Closeness rating is a measure of the distance between workstations in a facility layout. The rating is based on the frequency of movement between workstations, and it is used to determine the most efficient layout. A higher closeness rating indicates that workstations should be located closer together to reduce material handling costs and increase productivity.
Question 2: Compare and contrast product design and service design. Describe the objectives and phases of product design and development. Explain the importance of reliability in product design.
Answer: Product design and service design are two different approaches to creating a desirable user experience. Product design focuses on the development of tangible goods such as physical products, whereas service design emphasizes the design of intangible experiences and interactions between customers and service providers.
Objectives and Phases of Product Design and Development:
Product design and development involve a series of steps that aim to create a successful product that meets the needs of its intended market. The primary objective of product design is to create a product that is functional, aesthetically pleasing, and meets the needs of its users. The phases of product design and development typically include the following:
- Research and Analysis: In this phase, designers conduct research to identify the needs and preferences of their target audience, analyze the competitive landscape, and explore potential design solutions.
- Conceptualization: This phase involves brainstorming ideas, sketching concepts, and creating prototypes to test and refine design ideas.
- Design Development: In this phase, designers create detailed product specifications, refine the design, and develop prototypes that are tested and refined based on user feedback.
- Production: This phase involves the manufacturing of the final product and the creation of marketing materials and packaging.
- Launch: The product is introduced to the market and promoted to potential customers.
Importance of Reliability in Product Design:
Reliability is a critical aspect of product design as it relates to the consistency and dependability of a product’s performance over time. A reliable product is one that functions consistently and effectively over its expected lifespan, while an unreliable product is one that is prone to failure or malfunction.
The importance of reliability in product design cannot be overstated as it directly impacts a product’s overall quality and value to its users. A reliable product is more likely to satisfy its customers and gain a positive reputation, while an unreliable product can damage a company’s reputation and lead to lost sales and customer dissatisfaction.
Conclusion:
Product design and development and service design are two different approaches to creating a desirable user experience. The objectives and phases of product design and development include research and analysis, conceptualization, design development, production, and launch. Reliability is a critical aspect of product design, as it directly impacts a product’s overall quality and value to its users.
Question 3: Compare and contrast the different types of facility layouts, such as the repetitive product and process layouts, fixed position layout, and cellular layout. Discuss the factors that influence the choice of facility layout.
Answer: Facility layout refers to the arrangement of equipment, machinery, and other resources within a facility to facilitate efficient and effective production processes. There are several different types of facility layouts, each with its own unique advantages and disadvantages. The most common types of facility layouts include:
- Repetitive Product and Process Layouts: In repetitive product and process layouts, equipment and resources are arranged in a linear or U-shaped configuration, with the goal of maximizing efficiency and minimizing the distance that materials and products must travel between workstations. This layout is most commonly used in manufacturing settings where large volumes of standardized products are produced.
- Fixed Position Layouts: In a fixed position layout, the product being produced remains in one location, and workers and resources are moved to that location as needed. This layout is commonly used in construction projects and other large-scale operations.
- Cellular Layouts: A cellular layout involves the grouping of similar workstations into cells, with each cell dedicated to producing a specific product or product family. This layout is often used in industries where customized products are produced in small batches.
Factors that influence the choice of facility layout include:
- Production Volume: The volume of production can greatly influence the choice of facility layout. High-volume production environments are best suited for repetitive product and process layouts, while low-volume environments are better suited for cellular layouts.
- Product Design: The design of the product being produced can also impact facility layout decisions. For example, if a product requires specialized equipment or machinery, a fixed position layout may be the most appropriate choice.
- Flexibility: The level of flexibility required in production processes can also influence the choice of facility layout. A cellular layout provides greater flexibility to accommodate changes in product design or production volume, while a repetitive product and process layout is less flexible.
- Safety: Safety considerations also play a role in the choice of facility layout. For example, a fixed position layout may be preferable for projects that involve heavy equipment or machinery to minimize the risk of accidents.
Conclusion:
Facility layout is an important consideration in production processes. The choice of facility layout depends on various factors such as production volume, product design, flexibility, and safety. The most common types of facility layouts are repetitive product and process layouts, fixed position layouts, and cellular layouts, each with its own unique advantages and disadvantages.
Question 4: Define capacity planning and explain its significance in the production process. Calculate processing requirements and make or buy decisions. Apply CVP analysis to determine the break-even point for a business.
Answer: Capacity planning is the process of determining the production capacity required to meet the demand for a product or service, and ensuring that the production process can meet that demand. Capacity planning is significant in the production process because it helps companies ensure that they have the resources they need to meet demand, while avoiding overproduction or underproduction.
Significance of Capacity Planning:
- Meeting Demand: Capacity planning helps companies ensure that they have the resources they need to meet customer demand, minimizing the risk of stockouts or long lead times.
- Efficient Resource Allocation: Capacity planning helps companies allocate resources efficiently, avoiding overproduction or underproduction and minimizing waste.
- Cost Control: Effective capacity planning can help companies control costs by optimizing production processes, minimizing idle time, and reducing the need for overtime.
Processing Requirements:
Processing requirements refer to the amount of time and resources needed to complete a production process. To calculate processing requirements, companies need to know the demand for their products or services, as well as the time and resources required to produce them. This information can be used to determine the production capacity required to meet demand, and to identify any bottlenecks or constraints in the production process.
Make or Buy Decisions:
Make or buy decisions involve deciding whether to produce a product or service in-house or to outsource it to a third-party supplier. This decision depends on various factors such as the cost and availability of resources, production capacity, and the expertise required to produce the product or service.
CVP Analysis:
CVP (Cost-Volume-Profit) analysis is a financial tool used to determine the break-even point for a business, which is the point at which total revenues equal total costs. This analysis involves calculating the contribution margin, which is the difference between sales revenue and variable costs, and using this information to determine the break-even point.
To apply CVP analysis, companies need to know their fixed costs, variable costs, and the selling price of their products or services. By calculating the contribution margin, companies can determine the number of units they need to sell to break even, and the amount of revenue they need to generate to cover their fixed costs.
Conclusion:
Capacity planning is an important process in the production process that helps companies ensure that they have the resources they need to meet demand while minimizing costs and waste. Processing requirements, make or buy decisions, and CVP analysis are all tools that companies can use to optimize their production processes and achieve their financial goals.
Question 5: Define Supply Chain Management (SCM) and its benefits. Describe the different elements of SCM, such as logistics, EDI, and e-commerce. Discuss the requirements for effective SCM and the steps involved in optimizing it.
Answer: Supply Chain Management (SCM) refers to the coordination and management of activities involved in the production and delivery of goods and services from suppliers to customers. The primary objective of SCM is to ensure that products and services are delivered to customers in the most efficient and cost-effective manner.
Benefits of Supply Chain Management:
- Cost Reduction: SCM can help companies reduce costs by improving efficiency, reducing inventory, and minimizing waste.
- Improved Customer Service: SCM can help companies improve customer service by ensuring that products are delivered on time and in the correct quantity and quality.
- Increased Efficiency: SCM can help companies improve efficiency by optimizing production processes, reducing lead times, and improving coordination between suppliers and customers.
Elements of SCM:
- Logistics: Logistics involves the movement of goods and services from suppliers to customers, including transportation, warehousing, and inventory management.
- Electronic Data Interchange (EDI): EDI is a digital platform for exchanging business documents, such as purchase orders and invoices, between trading partners.
- E-commerce: E-commerce involves the buying and selling of goods and services over the internet, including online marketplaces and direct-to-consumer sales.
Requirements for Effective SCM:
- Clear Communication: Effective SCM requires clear and open communication between suppliers, manufacturers, and customers.
- Collaboration: Effective SCM requires collaboration between all parties involved in the supply chain, including suppliers, manufacturers, distributors, and customers.
- Efficient Information Management: Effective SCM requires efficient management of information, including accurate forecasting, inventory tracking, and logistics management.
Steps to Optimize SCM:
- Define Objectives: The first step in optimizing SCM is to define the company’s objectives and goals.
- Map the Supply Chain: The next step is to map the entire supply chain, including all the processes, resources, and stakeholders involved.
- Analyze Performance: The third step is to analyze the performance of the supply chain, including areas where costs can be reduced, and efficiency can be improved.
- Develop a Strategy: Based on the analysis, a strategy should be developed to optimize the supply chain, including identifying potential improvements in logistics, inventory management, and communication.
- Implement Changes: Finally, changes should be implemented to optimize the supply chain, including new technologies, process improvements, and changes in supplier relationships.
Conclusion:
Effective SCM is essential for companies to meet the demands of customers while minimizing costs and maximizing efficiency. SCM includes logistics, EDI, and e-commerce, and requires clear communication, collaboration, and efficient information management. Optimizing SCM involves defining objectives, mapping the supply chain, analyzing performance, developing a strategy, and implementing changes.
Question 6: Describe quality assurance and control and the methods used to ensure quality, such as inspection, statistical process control, control charts, and acceptance sampling. Explain the concept of Total Quality Control and the methods used for continuous improvement, such as KAIZEN and Six Sigma.
Answer: Quality assurance and quality control are two key concepts in the process of delivering high-quality products and services. Quality assurance refers to the set of processes used to ensure that products or services meet the specified requirements and standards, while quality control refers to the set of processes used to ensure that products or services meet the desired level of quality.
To ensure quality, organizations use various methods, such as inspection, statistical process control, control charts, and acceptance sampling.
Inspection involves examining products or services to identify defects or deviations from the required specifications. Statistical process control (SPC) involves monitoring a production process to identify and correct any variations or deviations from the desired level of quality. Control charts are graphical representations of process data that are used to track and monitor variations in the process over time. Acceptance sampling is a statistical technique that involves testing a sample of products or services to determine whether they meet the required specifications.
Total Quality Control (TQC) is a management approach that focuses on continuous improvement and the involvement of all employees in the quality improvement process. TQC involves identifying and eliminating the root causes of quality problems, promoting teamwork and collaboration, and continually improving processes.
KAIZEN is a Japanese term that means continuous improvement. It involves making small, incremental improvements to a process or system on an ongoing basis. KAIZEN emphasizes the involvement of all employees in the improvement process and focuses on identifying and eliminating waste, inefficiencies, and non-value-added activities.
Six Sigma is a data-driven approach to quality improvement that seeks to minimize defects and variations in a process or system. Six Sigma uses statistical methods and tools to measure and analyze process performance, identify the root causes of defects, and implement improvements to reduce defects and improve quality.
Conclusion:
Quality assurance and control involve ensuring that products or services meet the desired level of quality, and organizations use various methods such as inspection, statistical process control, control charts, and acceptance sampling to ensure quality. Total Quality Control, KAIZEN, and Six Sigma are methods used for continuous improvement to achieve high levels of quality and customer satisfaction.
Question 7: Discuss the challenges and opportunities in implementing a sustainable supply chain. What are the methods used to assess the sustainability of a supply chain, and how can organizations improve the sustainability of their supply chain?
Answer: Implementing a sustainable supply chain presents both challenges and opportunities for organizations. On one hand, sustainable supply chains can help organizations reduce costs, increase efficiency, improve their brand reputation, and comply with regulatory requirements. On the other hand, implementing a sustainable supply chain can be challenging due to the complexity of supply chains, the lack of transparency, and the difficulty in changing established practices and processes.
One of the key challenges in implementing a sustainable supply chain is identifying the most significant environmental and social impacts of the supply chain. Supply chains can have a significant impact on the environment, such as greenhouse gas emissions, water consumption, and waste generation. Additionally, supply chains can have social impacts, such as labor conditions and human rights violations. To address these impacts, organizations need to assess the sustainability of their supply chain and identify areas for improvement.
There are various methods used to assess the sustainability of a supply chain, such as:
- Life cycle assessment (LCA): This method involves analyzing the environmental impacts of a product or service throughout its entire life cycle, from raw material extraction to disposal.
- Environmental and social auditing: This involves conducting on-site inspections and audits of suppliers to evaluate their environmental and social performance.
- Supplier scorecards: These scorecards use key performance indicators (KPIs) to measure supplier performance in areas such as environmental management, labor practices, and supply chain transparency.
To improve the sustainability of their supply chain, organizations can take various steps such as:
- Implementing sustainable sourcing practices: This involves sourcing materials and products from suppliers that meet sustainability criteria and promote sustainable practices.
- Implementing circular economy practices: This involves designing products and processes to minimize waste and maximize resource efficiency.
- Engaging with suppliers: This involves working with suppliers to improve their sustainability performance and support their transition to sustainable practices.
- Building transparency and traceability: This involves increasing transparency and traceability in the supply chain to identify potential risks and opportunities for improvement.
- Collaborating with stakeholders: This involves working with stakeholders, such as customers, suppliers, and NGOs, to develop and implement sustainable supply chain initiatives.
Conclusion:
Implementing a sustainable supply chain presents both challenges and opportunities for organizations. To address these challenges, organizations can use various methods to assess the sustainability of their supply chain and take steps to improve their sustainability performance, such as implementing sustainable sourcing practices, circular economy practices, engaging with suppliers, building transparency and traceability, and collaborating with stakeholders.
Question 8: Discuss the different methods used for inventory classification, such as the ABC analysis and XYZ analysis. Explain how the results of inventory classification can be used to improve inventory management.
Answer:Inventory classification is the process of categorizing items in inventory based on their value or demand. By classifying inventory, organizations can prioritize the management of high-value or high-demand items and allocate resources more effectively. Two commonly used methods for inventory classification are ABC analysis and XYZ analysis.
ABC analysis involves classifying inventory items into three categories based on their annual usage value. The categories are:
- A items: These are high-value items that account for a small percentage of the total inventory but a significant percentage of the total value. These items should be closely monitored and managed to ensure availability.
- B items: These are moderate-value items that account for a moderate percentage of the total inventory and value. These items require a moderate level of management and monitoring.
- C items: These are low-value items that account for a large percentage of the total inventory but a small percentage of the total value. These items require minimal management and monitoring.
XYZ analysis involves classifying inventory items into three categories based on their demand variability and predictability. The categories are:
- X items: These are items with high demand variability and unpredictability. These items require careful management and monitoring to ensure availability.
- Y items: These are items with moderate demand variability and predictability. These items require a moderate level of management and monitoring.
- Z items: These are items with low demand variability and predictability. These items require minimal management and monitoring.
The results of inventory classification can be used to improve inventory management in several ways:
- Resource allocation: By focusing on high-value or high-demand items, organizations can allocate resources more effectively and ensure that these items are always available.
- Inventory control: By closely monitoring and managing high-value or high-demand items, organizations can reduce the risk of stockouts and overstocking.
- Supplier management: By identifying high-value or high-demand items, organizations can work closely with suppliers to ensure that these items are always available and that lead times are minimized.
- Process improvement: By identifying and analyzing inventory patterns and trends, organizations can improve their inventory management processes and identify opportunities for cost savings and efficiency improvements.
Conclusion:
Inventory classification is a useful tool for organizations to prioritize the management of high-value or high-demand items and allocate resources more effectively. ABC analysis and XYZ analysis are two commonly used methods for inventory classification, and the results of inventory classification can be used to improve inventory management by optimizing resource allocation, inventory control, supplier management, and process improvement.
Question 9: Discuss the different purchasing interfaces and the purchasing cycle. Compare and contrast centralized and decentralized purchasing. Explain the importance of value analysis in purchasing and the ethical issues in purchasing.
Answer: Purchasing interfaces refer to the different methods by which organizations interact with suppliers to procure goods and services. The main purchasing interfaces are:
- Direct purchasing: This involves buying goods and services directly from a supplier without the involvement of a middleman or distributor.
- E-procurement: This involves using electronic platforms and systems to manage the purchasing process, such as online catalogs, e-auctions, and e-marketplaces.
- Outsourcing: This involves contracting with a third-party service provider to manage the procurement process on behalf of the organization.
The purchasing cycle refers to the series of steps involved in the procurement process, from identifying the need for goods and services to making payment to suppliers. The main stages of the purchasing cycle are:
- Need identification: This involves identifying the need for goods or services and determining the quantity and quality required.
- Vendor selection: This involves selecting a supplier or vendors that can meet the organization’s requirements.
- Purchase order generation: This involves issuing a purchase order to the supplier, specifying the quantity, quality, price, and delivery date of the goods or services.
- Receipt of goods or services: This involves verifying that the goods or services received from the supplier meet the organization’s requirements.
- Invoice processing: This involves processing and approving the supplier’s invoice for payment.
Centralized purchasing refers to a purchasing structure where all purchasing decisions and activities are centralized in one department or individual. Decentralized purchasing, on the other hand, refers to a structure where purchasing decisions and activities are spread out across different departments or individuals within the organization.
The importance of value analysis in purchasing lies in its ability to help organizations identify and evaluate the total cost of ownership of goods and services, including the cost of acquisition, use, maintenance, and disposal. By conducting value analysis, organizations can identify opportunities for cost savings, improve the quality of goods and services, and make more informed purchasing decisions.
Ethical issues in purchasing include issues related to supplier selection, supplier relations, and supplier practices. For example, ethical issues may arise when an organization selects a supplier based on personal relationships or when a supplier engages in unethical practices such as bribery or human rights violations. To address these issues, organizations need to establish ethical guidelines for supplier selection and engagement and monitor supplier practices regularly. Additionally, organizations should conduct due diligence on suppliers to ensure that they meet ethical standards and comply with applicable laws and regulations.
Question 10: Discuss the importance of ethical considerations in purchasing. Describe the different ethical issues that can arise in the purchasing process and the methods used to address them.
Answer: Ethical considerations are crucial in purchasing because purchasing decisions and practices can have a significant impact on stakeholders such as suppliers, customers, employees, and society as a whole. Ethical issues in purchasing can arise at any stage of the procurement process and can include issues related to supplier selection, pricing, contracting, payment, and post-contractual relationships.
Some of the different ethical issues that can arise in the purchasing process include:
- Supplier selection: Ethical issues can arise when selecting suppliers based on personal relationships or when suppliers engage in unethical practices such as bribery or human rights violations.
- Pricing: Ethical issues can arise when suppliers engage in price fixing or when organizations engage in predatory pricing or price gouging.
- Contracting: Ethical issues can arise when contracts are not negotiated in good faith, when contracts are not fulfilled as agreed, or when contracts contain unfair or unethical terms.
- Payment: Ethical issues can arise when payment is delayed or withheld for unjustified reasons or when payment is made to suppliers that engage in unethical practices.
To address these issues, organizations can take several steps, including:
- Establishing ethical guidelines: Organizations can establish ethical guidelines for supplier selection, engagement, and conduct that align with their values and principles.
- Conducting due diligence: Organizations can conduct due diligence on suppliers to ensure that they meet ethical standards and comply with applicable laws and regulations.
- Monitoring supplier practices: Organizations can monitor supplier practices regularly to identify and address any unethical behavior.
- Training employees: Organizations can provide training to employees on ethical practices and guidelines for purchasing to promote ethical behavior.
- Establishing whistleblower mechanisms: Organizations can establish mechanisms for employees to report unethical behavior without fear of retaliation.
Conclusion:
Ethical considerations are essential in purchasing, and ethical issues can arise at any stage of the procurement process. To address these issues, organizations need to establish ethical guidelines, conduct due diligence, monitor supplier practices, provide employee training, and establish whistleblower mechanisms. By promoting ethical behavior in purchasing, organizations can protect stakeholders’ interests, enhance their reputation, and contribute to sustainable and responsible business practices.
Question 11: Discuss the legal and environmental issues related to product and service design. How can organizations address these issues?
Answer: Legal and environmental issues related to product and service design have become increasingly important for organizations in recent years. These issues can have significant impacts on the success and reputation of businesses, as well as the environment and society as a whole.
Legal issues related to product and service design include issues such as product liability, intellectual property infringement, and regulatory compliance. Businesses need to ensure that their products and services are safe for consumers and comply with applicable laws and regulations. Failure to do so can result in legal action and damage to the company’s reputation.
Environmental issues related to product and service design include issues such as resource depletion, pollution, and climate change. Organizations have a responsibility to minimize the environmental impact of their products and services throughout their lifecycle, from raw material extraction to disposal.
To address these issues, organizations can take several steps. One approach is to incorporate sustainability into the product design process. This can involve using environmentally friendly materials, designing products that are easy to repair and recycle, and minimizing packaging waste. Organizations can also work with suppliers to ensure that they meet environmental standards and prioritize sustainable practices.
Another approach is to conduct regular risk assessments to identify potential legal and environmental issues related to product and service design. This can help organizations to identify potential issues before they arise and take steps to mitigate them.
Finally, organizations can engage with stakeholders, including customers, regulators, and environmental groups, to better understand their concerns and develop solutions that meet their needs. By incorporating stakeholder feedback into the product design process, organizations can develop products and services that are both environmentally responsible and legally compliant.
Conclusion:
Legal and environmental issues related to product and service design are important considerations for organizations. By incorporating sustainability into the product design process, conducting regular risk assessments, and engaging with stakeholders, organizations can address these issues and develop products and services that meet the needs of both their customers and the environment.
Question 12: Explain the concept of automation in Operations Management. What are the benefits and challenges of automation in a production system?
Answer: Automation in Operations Management refers to the use of technology and machines to perform tasks that were previously done manually by humans. It involves the integration of hardware and software to automate processes, reducing human intervention and increasing efficiency.
The benefits of automation in a production system include:
- Increased Efficiency: Automation can perform tasks much faster than humans, leading to increased productivity and throughput. This helps organizations to meet demand and deliver products to customers in a timely manner.
- Improved Quality: Automated systems can perform tasks with a higher degree of accuracy and consistency, leading to improved product quality and fewer defects.
- Reduced Labor Costs: By automating tasks, organizations can reduce the need for human labor, leading to reduced labor costs and improved profitability.
- Increased Safety: Automation can perform tasks that are too dangerous for humans, leading to a safer working environment for employees.
However, there are also challenges associated with automation in a production system, including:
- High Initial Investment: Implementing an automated production system requires a significant investment in equipment and software, which can be costly for organizations.
- Technical Complexity: Automated systems can be complex and require specialized knowledge to operate and maintain. This can be a challenge for organizations that do not have the necessary expertise.
- Reduced Flexibility: Automated systems are designed to perform specific tasks, and can be less flexible than manual labor in responding to changes in production requirements.
- Potential Job Losses: The use of automation can lead to a reduction in the number of jobs available for humans, potentially leading to job losses and social impacts.
Conclusion:
Automation in Operations Management can provide significant benefits for organizations, including increased efficiency, improved quality, reduced labor costs, and increased safety. However, it also presents challenges, such as high initial investment, technical complexity, reduced flexibility, and potential job losses. Organizations should carefully evaluate the costs and benefits of automation before implementing an automated production system.
Question 13: Explain the concept of CVP analysis and its relevance in capacity planning. Provide a real-life example to demonstrate the application of CVP analysis.
Answer: CVP analysis stands for Cost-Volume-Profit analysis, and it is a financial tool used to determine the relationship between the cost of producing a product, the volume of production, and the resulting profit. CVP analysis can help businesses understand how changes in these factors affect their profits, and make decisions about pricing, production levels, and cost management.
In capacity planning, CVP analysis is used to determine the optimal level of production to maximize profits. By analyzing the costs associated with producing a product at different levels of production, businesses can identify the point where the revenue generated from sales equals the cost of producing the product, and the profit is maximized. This is known as the break-even point.
CVP analysis takes into account three main components:
- Fixed Costs: These are costs that do not vary with the level of production, such as rent, salaries, and insurance.
- Variable Costs: These are costs that increase or decrease with the level of production, such as raw materials, labor, and energy.
- Selling Price: This is the price at which the product is sold to customers.
By analyzing the relationship between these three components, businesses can determine the level of production that will result in the maximum profit.
For example, let’s consider a business that produces and sells widgets. The fixed costs associated with producing widgets are Rs.1,00,000 per month, and the variable costs per unit are Rs.50. The selling price per unit is Rs.200. Using CVP analysis, the break-even point can be calculated as follows:
- Break-even point = Fixed Costs / (Selling Price – Variable Costs)
- Break-even point = Rs.1,00,000 / (Rs.200 – Rs.50)
- Break-even point = 667 units
This means that the business needs to produce and sell at least 667 units of widgets per month to break even. If the business produces and sells more than 667 units, it will generate a profit. If it produces and sells less than 667 units, it will incur a loss.
CVP analysis can be used to determine the optimal level of production to maximize profits, by analyzing the costs associated with producing a product at different levels of production, and comparing it with the revenue generated from sales. By using CVP analysis, businesses can make informed decisions about pricing, production levels, and cost management.
Question 14: Explain the concept of ISO quality systems, such as ISO 9000 and ISO 14000. What are the benefits of ISO certification for an organization?
Answer: ISO quality systems refer to a series of international standards developed by the International Organization for Standardization (ISO) to ensure consistent quality and environmental management practices across industries and geographic regions. The two most widely recognized ISO quality systems are ISO 9000 and ISO 14000.
ISO 9000 is a quality management system standard that outlines the requirements for an organization to meet customer and regulatory requirements, enhance customer satisfaction, and continually improve its processes. ISO 14000 is an environmental management system standard that helps organizations identify and control their environmental impact and comply with relevant regulations.
The benefits of ISO certification for an organization include:
- Improved Credibility: ISO certification is widely recognized and respected in many industries, which can improve an organization’s reputation and credibility with customers, suppliers, and regulatory bodies.
- Enhanced Customer Satisfaction: By implementing ISO quality systems, organizations can better understand customer needs and expectations, and deliver products and services that meet or exceed those expectations.
- Better Efficiency and Productivity: ISO quality systems can help organizations identify and eliminate inefficiencies and waste in their processes, leading to better productivity and cost savings.
- Improved Environmental Performance: ISO 14000 certification can help organizations reduce their environmental impact and improve sustainability, which is becoming increasingly important for many customers and stakeholders.
- Competitive Advantage: ISO certification can help organizations differentiate themselves from competitors and gain a competitive advantage in the market.
- Access to New Markets: Some industries and regions require ISO certification for organizations to participate in certain contracts or business opportunities, which can open up new markets and opportunities for growth.
Conclusion:
ISO quality systems, such as ISO 9000 and ISO 14000, provide a framework for organizations to ensure consistent quality and environmental management practices, leading to improved credibility, customer satisfaction, efficiency, productivity, and competitiveness. ISO certification can also provide access to new markets and business opportunities.
Question 15: Explain the concept of Lean Operations and its application in service organizations. What are the benefits of Lean Operations for service organizations?
Answer: Lean operations refer to a systematic approach to operations management that aims to optimize efficiency, reduce waste, and improve the overall quality of operations. The goal of lean operations is to provide value to customers while minimizing waste, and it involves continuously reviewing and improving processes to eliminate inefficiencies and unnecessary steps.
In service organizations, lean operations can be applied to various areas, including customer service, order processing, and supply chain management. The principles of lean operations can help service organizations to streamline their operations, reduce costs, improve quality, and enhance customer satisfaction.
Some of the benefits of implementing lean operations in service organizations include:
- Improved efficiency: Lean operations can help service organizations to streamline their operations and eliminate unnecessary steps, resulting in improved efficiency and productivity.
- Reduced costs: By eliminating waste and improving efficiency, service organizations can reduce costs associated with unnecessary steps, rework, and delays.
- Improved quality: Lean operations can help service organizations to identify and eliminate defects, resulting in improved quality of service and customer satisfaction.
- Enhanced customer satisfaction: By improving the quality of service, reducing wait times, and addressing customer needs, service organizations can enhance customer satisfaction and loyalty.
- Increased flexibility: Lean operations can help service organizations to respond quickly to changing customer demands and market conditions, enabling them to adapt and thrive in a rapidly changing environment.
Conclusion:
Lean operations can provide significant benefits to service organizations, including improved efficiency, reduced costs, improved quality, enhanced customer satisfaction, and increased flexibility. By adopting a lean operations approach, service organizations can optimize their operations and provide greater value to their customers.
Question 16: Explain the concept of logistics in Supply Chain Management. What are the different modes of transportation used in logistics, and what are their advantages and disadvantages?
Answer: Logistics is an essential component of supply chain management that involves the planning, implementation, and control of the movement of goods, information, and resources from the point of origin to the point of consumption. Logistics includes a range of activities, such as transportation, warehousing, inventory management, and orders processing that are aimed at achieving the timely and cost-effective delivery of products or services.
Transportation is one of the critical elements of logistics, and it involves the movement of goods from one location to another. There are several modes of transportation that are used in logistics, including:
- Road Transportation: This includes trucks, vans, and other vehicles that operate on roads. Road transportation is often the most common and flexible mode of transportation, suitable for short and medium distances, and provides direct delivery to the destination. However, it is also subject to traffic congestion, delays, and road infrastructure conditions.
- Rail Transportation: This mode of transportation is suitable for long distances, bulky goods, and heavy materials. It is often cheaper than other modes of transportation and is more environmentally friendly. However, it is less flexible than road transportation, and rail transport requires additional transportation modes to deliver goods to the final destination.
- Air Transportation: Air transportation is the fastest mode of transportation and is suitable for high-value, time-sensitive goods. It can deliver goods to any part of the world, but it is also the most expensive mode of transportation.
- Water Transportation: This mode of transportation includes ships, barges, and other vessels that operate on waterways. Water transportation is suitable for long distances, bulky goods, and low-value items. However, it is also the slowest mode of transportation and is subject to weather conditions, port congestion, and other delays.
The advantages and disadvantages of each mode of transportation depend on various factors, such as the distance, type of goods, delivery time, and cost. For example, road transportation is suitable for short distances and provides direct delivery, but it is subject to congestion and delays. Air transportation is suitable for time-sensitive goods, but it is expensive. Rail transportation is suitable for long distances and bulky goods, but it requires additional transportation modes to deliver goods to the final destination. Water transportation is suitable for long distances and low-value items, but it is slow and subject to weather conditions.
Conclusion:
Logistics is a critical component of supply chain management that involves the movement of goods from one location to another. There are several modes of transportation used in logistics, each with its advantages and disadvantages, and the selection of the mode of transportation depends on various factors such as distance, type of goods, delivery time, and cost.
Question 17: Explain the concept of Operations Management and its relationship with other management functions. Discuss the role of production management in the operations function. Compute the productivity of a production system.
Answer: Operations management refers to the process of managing all aspects of the production of goods or services within an organization. It is concerned with the planning, organizing, and controlling of resources to achieve efficient and effective output.
The role of operations management is closely related to other management functions such as marketing, finance, and human resources. Marketing provides information about customer needs and preferences, which helps operations management to plan production accordingly. Finance provides the resources necessary for operations management to carry out its plans, while human resources provide the skilled workforce required to carry out the production.
Production management is a key component of operations management. It is concerned with the planning, organizing, and controlling of the production process. Production managers are responsible for ensuring that goods or services are produced efficiently and effectively, meeting quality standards and customer requirements.
Productivity is an important measure of the efficiency of a production system. It is defined as the ratio of output to input. The productivity of a production system can be calculated using the following formula:
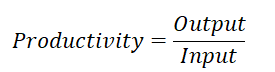
For example, if a factory produces 1000 units of a product using 10 workers and 8 hours of work per day, the productivity of the production system can be calculated as:

= 12.5 units per worker per hour
By measuring productivity, production managers can identify areas for improvement and implement strategies to increase efficiency and effectiveness.
Question 18: Explain the concepts of JIT and lean operations. Describe the application of JIT in services and its benefits.
Answer: JIT (Just-In-Time) and lean operations are related concepts that aim to minimize waste and maximize efficiency in the production or delivery of goods or services.
JIT involves producing or delivering goods or services just in time to meet customer demand, without holding any excess inventory or having any excess capacity. This means that production or delivery processes are tightly synchronized, and inventory is only replenished when needed. JIT relies on a highly responsive and efficient supply chain, with suppliers delivering materials and components just in time for production.
Lean operations, on the other hand, are broader in scope and involve a continuous process of identifying and eliminating waste in all aspects of the production or delivery process. This includes reducing defects, minimizing waiting times, and streamlining processes. Lean operations aim to maximize value for the customer while minimizing costs and resources.
JIT can also be applied to services, where it is known as Just-In-Time services (JITS). JITS involves providing services just in time to meet customer demand, without requiring customers to wait or have excess capacity. This can be achieved by optimizing service processes, scheduling appointments or reservations, and using technology to facilitate efficient service delivery.
The benefits of JIT and lean operations include reduced lead times, increased quality, improved efficiency, and lower costs. JIT can also result in reduced inventory holding costs and lower storage requirements, while lean operations can result in improved customer satisfaction and increased competitiveness.
In services, the benefits of JIT include reduced waiting times, increased customer satisfaction, and improved service quality. JITS can also result in lower operating costs, as services are only provided when needed, and can facilitate better resource utilization and planning.
Overall, JIT and lean operations are powerful tools for achieving operational excellence, and their application in both manufacturing and services can result in significant benefits for organizations and their customers.
Question 19: Explain the importance of inventory management and control. Describe the different inventory costs and the ABC analysis. Calculate the EOQ and the economic production quantity model.
Answer: Inventory management and control are essential for any organization that deals with the production, storage, and distribution of goods. Effective inventory management ensures that the right products are available in the right quantities at the right time, minimizing costs and maximizing customer satisfaction.
Inventory costs can be broadly categorized into three types: holding costs, ordering costs, and shortage costs. Holding costs refer to the costs of storing and maintaining inventory, including storage costs, insurance, and obsolescence. Ordering costs refer to the costs of ordering and receiving inventory, including administrative costs, transportation, and inspection. Shortage costs refer to the costs of stockouts, including lost sales, customer dissatisfaction, and rush orders.
The ABC analysis is a popular inventory management technique that involves classifying inventory items based on their value and importance. A items are high-value items that account for a large proportion of total inventory value but a small proportion of total inventory volume. B items are moderate-value items that account for a moderate proportion of total inventory value and volume. C items are low-value items that account for a small proportion of total inventory value but a large proportion of total inventory volume. The ABC analysis can be used to prioritize inventory management efforts and allocate resources accordingly.
The Economic Order Quantity (EOQ) is a mathematical model used to determine the optimal order quantity that minimizes total inventory costs. The EOQ model considers two types of costs: ordering costs and holding costs. The formula for EOQ is:
EOQ = sqrt((2 x D x O) / H)
where D is the annual demand, O is the ordering cost, and H is the holding cost per unit per year.
The Economic Production Quantity (EPQ) model is similar to the EOQ model but takes into account the production rate and the setup cost. The formula for EPQ is:
EPQ = sqrt((2 x D x S) / H)
where S is the setup cost.
Both the EOQ and EPQ models can be used to optimize inventory management and control, ensuring that inventory levels are maintained at an optimal level to minimize costs while meeting customer demand.
Question 20: Explain the need for location decisions and the factors affecting them. Describe the different methods used for site selection, such as the factor rating method, the center of gravity method, and the least cost method.
Answer: Location decisions are crucial for the success of any business. Choosing the right location can affect a company’s cost structure, competitiveness, and access to markets and resources. Location decisions also involve long-term commitments and significant capital investment, making it important to carefully consider various factors and methods when making a decision.
Factors affecting location decisions can be broadly categorized into three types: economic, social, and political. Economic factors include costs of labor, transportation, utilities, taxes, and proximity to markets and suppliers. Social factors include demographics, cultural norms, quality of life, and availability of skilled labor. Political factors include regulations, government incentives, and stability of the legal and regulatory environment.
There are several methods used for site selection, each with its strengths and weaknesses. The factor rating method involves identifying relevant factors and assigning weights to them based on their importance. Each potential site is then evaluated on each factor, and scores are assigned based on how well they meet the criteria. The scores are then weighted, and the site with the highest total score is selected.
The center of gravity method involves identifying the locations of customers or suppliers and calculating the center of gravity based on their relative distances. The optimal location is then determined based on the proximity to the center of gravity.
The least cost method involves identifying potential sites and calculating the total cost of transportation, labor, utilities, taxes, and other relevant factors. The site with the lowest total cost is selected.
Other methods include the transportation model, which uses linear programming to optimize transportation costs, and the analytical hierarchy process, which involves identifying and prioritizing criteria and alternatives based on their relative importance.
Conclusion:
Location decisions are important for any business, and factors affecting location decisions can be economic, social, and political. Different methods, such as the factor rating method, the center of gravity method, and the least cost method, can be used to select the optimal site based on relevant criteria.
Question 21: In a production unit, the standard time allowed for the production of a unit is 5 hrs. If in a particular month 126 units are produced by employing 4 persons and the allowable delays are found to be 44 man-hours, calculate the productivity and wastivity of the concern.
Answer:
ESH = Earned Standard Hours
STD Time/Unit = 5 hrs
Production = 126 units
Earned standard man-hours = 5 × 126 = 630 hrs
AMH = Available Man-hours
Manpower Employed = 4 P
Monthly working hrs = 4 × 25 × 8 = 800 hrs
Allowed delays = 44 hrs
Therefore,
AMH = Actual Man-hours available for production
= (800 – 44) hrs
= 756 hrs.
Now,
Productivity = (ESH/AMH) × 100
= (630/756) × 100
= 83.33%
Wastivity = 100 – 83.33
= 16.67%
Total Views: 53