Answer:
Supply chain management involves proactively managing the two-way movement and coordination (that is, the flows) of goods, services, information, and funds from raw material through end user. A company with a “supply chain orientation” is one that recognizes the strategic value of managing operational activities and flows across a supply chain. Its decisions fall into three categories or phases:
Supply Chain Design
Supply Chain Design is a strategic decision. It reflects the structure of the supply chain over the next several years. It decides what the chain’s configuration will be, how resources will be allocated, and what processes each stage will perform.
Successful design requires a high degree of functional and organizational integration. In order to do so, it is essential to develop supply chain process maps (flow charts) for major supply chains and their related processes helps establish an understanding of the supply chain. There should be a clearly understood mapping convention to be utilized, along with other information requirements. The objective of this exercise is to develop supply chain maps that present all supply chain entities along with key processes.
From this exercise will flow such decisions as the location and capacities of production and warehousing facilities, the products to be manufactured or stored at various locations, the modes of transportation, and the type of information system to be utilized. The organization must also identify key and critical supply chains components. It must be knowledgeable regarding its part of the supply chain and also must understand how the part interfaces with the other parts of the supply chain.
The supply chain configuration should support the organization’s strategic objectives.
Example: In the case of TI Cycles discussed in Module 1, its decisions regarding the location and capacity of its manufacturing facilities at Aurangabad, the joint manufacturing agreement with Avon Cycles and distribution network are all supply chain design or strategic decisions.
These are long-term decisions and are very expensive to alter on short notice. Consequently, when companies make these decisions, they must take into account uncertainty in anticipated market conditions over the next few years.
Supply Chain Planning
In the planning phase, companies define a set of operating policies that govern short-term operations and are normally determined on an annual basis. These decisions are made within the supply chain’s configuration. Planning starts with a demand forecast for the coming year. Based on the demand, an annual plan is worked out. Decisions regarding which markets will be supplied from which locations, outsourcing and sub-contracting, inventory policies, etc. are made. Planning, in other words, establishes parameters within which a supply chain will function over a specified period of time.
Once the key supply chains have been identified, one must identify the supply chain member organizations (suppliers and customers) that are considered most critical to the organization’s supply chain management efforts. In selecting external members, several issues should be addressed.
- SCM endeavors are likely to be more productive if participating organizations are not direct competitors. There may be limits to collaborative supply chain efforts when both buyer-supplier and competitor relationships exist between participating organizations.
- All organizations and their representatives must be pursuing similar goals. This does not mean that each organization should have identical goals, but that their respective goals must be compatible with the overall SCM initiative.
- SCM initiative is unlikely to be successful unless all members from each organization involved feel they are benefiting from participation. SCM efforts have to be focused where the involvement is beneficial to all the members.
In well managed organizations, in the planning phase uncertainty in demand, exchange rates, and competition over this time horizon are included in the decisions. Given a shorter time horizon and better forecasts than the design phase, the planning phase tries to exploit the supply chain design to optimize performance.
Supply Chain Operation
This has a short-term time horizon, monthly, weekly or daily. The focus, during this phase, is on individual customer orders. At the operational level, within planning policies, the goal is to handle incoming customer orders in the best possible manner. Firms allocate inventory or production to individual orders, set a date that an order is to be filled, generate pick lists at a warehouse, allocate an order to a particular shipping mode and shipment, set delivery schedules of trucks, and place replenishment orders.
Aggregate planning is the basis for decisions at this stage. The aggregate plan serves as a broad blueprint for operations and establishes the parameters within which short-term production and distribution decisions are made. It allows the supply chain to alter capacity allocations and change supply contracts. In addition, many constraints that must be considered in aggregate planning come from supply chain partners outside the enterprise, particularly upstream supply chain partners. Without these inputs from both up and down the supply chain, aggregate planning cannot realize its full potential to create value.
The output from aggregate planning is also of value to both upstream and downstream partners. Production plans for an organization define demand from suppliers and establish supply constraint for customers. If a manufacturer has planned an increase in production over a given time period, the supplier, the transporter, and warehousing partner must be aware of this plan and incorporate the increase in their own plans.
Because operation decisions are being made in the short term, there is less uncertainty about demand information. Given the constraints established by the configuration and planning policies, the goal during the operation phase is to exploit the reduction of uncertainty and optimize performance.
Ideally, all stages of the supply chain should work together to optimize supply chain performance. An important supply chain issue is collaboration with down stream supply chain partners. Slack of co-ordination will result in shortages or oversupply in the supply chain. Therefore, it is important to perform aggregate plans over as wide a scope of the supply chain as is reasonably possible.
1. Internal Supply Chains
The internal supply chain is that portion of a given supply chain that occurs within an individual organization. The first step in moving towards supply chain management is to develop these internal chains. Internal supply chains can be quite complex. Given the multidivisional, international organizational structures found in many businesses, it is not uncommon for the internal part of a supply chain to have multiple “links” that span the globe. Developing an understanding of the organization’s internal supply chain is often an appropriate starting point for firms considering an SCM initiative.
In these multi-divisional structures, the employees of one division often view the “other” divisions in much the same manner as they would external suppliers or customers. In some cases, turf wars between divisions make integrating cross-divisional functions and processes very difficult.
The supply chain has to be seen as a set of interrelated processes rather than a series of discrete, non-aligned activities. Process maps are developed to understand the overall internal supply chain linkages. These maps provide the basic information required to link the different entities. Examples of key processes and associated entities include order information from sales, order entry for materials planning, order preparation by purchasing, manufacturing, or warehousing, and order shipment for distribution and transportation. Each key process is documented along with current performance information.
It is beneficial when the different divisions understand the steps in their portion of the supply chain and “what happens” outside their part of the process. Developing supply chain process maps (flow charts) for major supply chains and their related processes is a basic requirement to establish an effective supply chain.
2. External Supply Chains
Once one understands the internal supply chain, one must extend the analysis to the external portion of the supply chain (i.e., key suppliers and customers). This is an important step, as significant opportunities for improvement often lie at the interfaces between the various supply chain member organizations. This step also adds a greater level of complexity, given that multiple organizations and their representatives are now participating in the analysis.
At this point in the analysis, the organization needs to focus its efforts on those supply chains that are most important to the organization’s success. The organization determines which products should be produced internally or purchased. Once the decision is made to purchase a product or service from external suppliers, purchasing is brought into the process.
3. Supply Chain Processes
The management of the supply chain covers everything from product development, sourcing, production, and logistics, as well as the information systems needed to co-ordinate inventory, cost, information, customer service, and collaboration relationships. A supply chain is a sequence of processes and flows that take place within and between different stages and combine to fill a customer need for a product.
Push/Pull View of Supply Chain
Processes in a supply chain are divided into two categories depending on whether they are executed in response to a customer order or in anticipation of customer orders. Pull processes are initiated by a customer order whereas push processes are initiated and performed in anticipation of customer orders.
Example: Tata Steel that collects orders that are similar enough to enable the manufacturer to produce in large quantities. In this case, the manufacturing cycle is reacting to customer demand (referred to as a pull process).
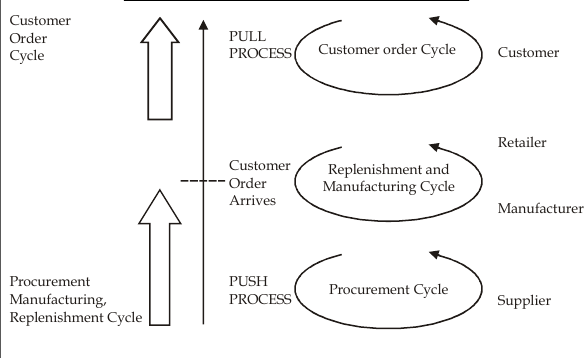
Hindustan Lever Ltd. a consumer products firm, which must produce in anticipation of demand. In this case, the manufacturing cycle is anticipating customer demand (referred to as a push process).
Figure 1 shows graphically the push/pull system in a retail network. It can be clearly seen from the figure that in the pull processes, customer demand is known with certainty at the time of execution, i.e., it is executed after the customer order arrives, whereas for a push process, demand is not known and must be forecast as the customer order is yet to arrive. Therefore, pull processes may also be referred to as reactive processes because they react to customer demand. Push processes may also be referred to as speculative processes because they respond to forecasted rather than actual demand. The push/pull boundary in a supply chain separates push processes from pull processes.
A push/pull view of the supply chain is very useful when considering strategic decisions relating to supply chain design. This view forces a more global consideration of supply chain process as they relate to a customer order. For instance, it could result in responsibility for certain processes being passed on to a different stage of the supply chain if making this transfer allows push process to become a pull process. One clear distinction between the two supply processes is that a supply chain that has fewer stages and more pull processes has a significant impact on improving supply chain performance.